Energia Renovável é destaque da 31ª Senafor
Evento abordou os últimos avanços no setor de conformação mecânica, metalurgia do pó e a estreia da modalidade que envolve materiais e processos para a produção de energias renováveis
Este ano foi o início de uma nova etapa para a Senafor, que completou sua 31ª edição em Porto Alegre, de 5 a 7 de outubro. Cerca de 450 pessoas conferiram a 1ª Conferência Internacional de Materiais e Processos para Energias Renováveis, focado na área metal-mecânica. Profissionais do setor, professores, pesquisadores e estudantes, - muitos vindos de outros países como Alemanha, Estados Unidos, Japão, Bélgica, China, Polônia, Portugal entre outros –, fizeram visitas técnicas, assistiram palestras voltadas para conformação mecânica e metalurgia do pó, além de se aprimorarem profissionalmente por meio das inovações tecnológicas e trabalhos científicos apresentados.
Paralelamente ao evento, as empresas atuantes no setor apresentaram informações sobre máquinas, equipamentos, softwares e serviços. Aconteceu também a premiação de incentivo acadêmico/científico, em que se destacaram os trabalhos de “Otimização do processo de forjamento através da análise termográfica”, de Henri Strasser, da Henkel, melhor trabalho da indústria; e “Six-Sigma Methodology Approach For Forgin Process”, conquistado pelo engenheiro Mauricio Santaella, da Universidade Técnica de Aachen (Alemanha) na área acadêmica.
A 32ª Senafor acontecerá de 9 a 11 outubro de 2012, também no Centro de Eventos Plaza São Rafael, em Porto Alegre.
.jpg)
|
O Deus do vento
Atribui-se a Éolo, personagem da mitologia grega, o título de Deus dos ventos, daí a razão para a energia gerada pela força dos ventos ter o nome de “eólica”. Este foi o foco da nossa equipe de reportagem no primeiro dia do Senafor, que esteve na cidade de Osório, de 40 mil habitantes, situada a 90 quilômetros de capital gaúcha. A região dispõe de uma privilegiada combinação de fatores que a torna um marco no campo energético limpo.
Desde 2007, este município abriga um impressionante parque eólico, sendo o maior da América Latina. Trata-se de um complexo composto de 75 aerogeradores, torres de 800 toneladas cada, com cerca de 98 metros de altura, sendo que somado as hélices, de 35 metros cada, eleva-se ao patamar de 133 metros do chão, fora a parte aterrada de 36 metros de profundidade. Sua produção total pode alcançar cerca de 150 megawatt (MW), suficiente para atender a demanda de uma cidade de 700 mil habitantes.
Trata-se de um empreendimento da Ventos do Sul Energia, propriedade da espanhola Enerfi n/Enervento, da alemã Wobben e da brasileira CIP Brasil. Foram investidos cerca de R$ 670 milhões, onde 69% saíram dos cofres do Banco Nacional de Desenvolvimento Econômico e Social, BNDES.
|
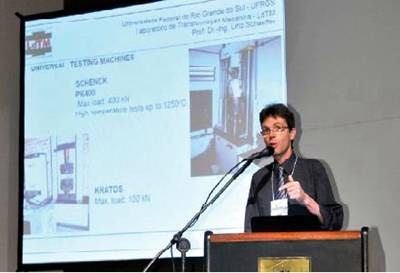
O professor e doutor Lírio Schaeffer, presidente da comissão organizadora do evento, abriu os trabalhos, passando a palavra em seguida para Peterson Ferrandini (foto) que apresentou uma síntese sobre o que é o Laboratório de Transformação Mecânica, LdTM,
parte da Universidade Federal do Rio Grande do Sul.
|
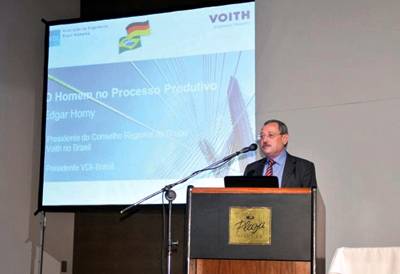
“O homem no processo produtivo”, por Edgar Horny, presidente do conselho regional da Voith Brasil, destacou a importância de ampliar a valorização do capital humano, apresentando comparativos entre investimentos em máquinas e equipamentos versus folha salarial, onde esta segunda apresenta declínio. Estudo indica que a preparação mais efi caz gerou uma redução de 13% para 1,7% no número de acidentes do trabalho. Um episódio na Coreia do Sul foi citado para ilustrar como uma simples ação de colocar uma fotografia do operador na máquina em que atua, como se ele fosse o proprietário, gerou uma significativa melhora em limpeza e outros cuidados.
|
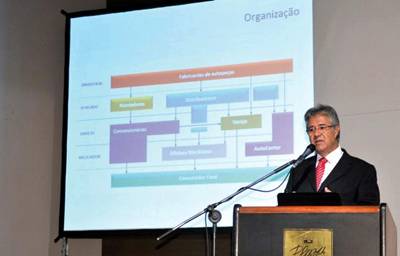
“O mercado de reposição de autopeças no Brasil”, por Antônio Carlos Bento, do Sindipeças e CEO das indústrias Corneta, apresentou um panorama sobre o número de empresas no setor de autopeças no país e os reflexos da importação, onde os números indicam que no Brasil, em 2006, ocorreu um superávit de US$ 2 bilhões. A previsão do especialista é que ao fechar 2011 alcançaremos US$ 4 bilhões de déficit.
|
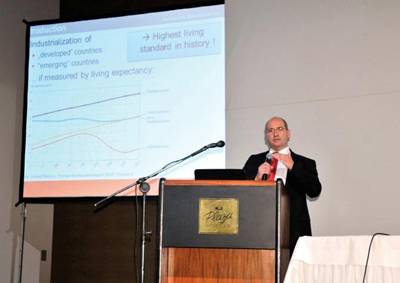
“Manufatura suportada por processo de simulação”, por Hendrik Schafstall, da Simufact (Alemanha), focou as mudanças geopolíticas, o crescimento populacional, a ausência de sustentabilidade e a explosão do conhecimento. As análises indicam necessidades e vantagens da otimização nos processos produtivos (antes, durante e depois) como forma de ampliar a eficiência em fazer produtos mais arrojados, econômicos, com mínimo de desperdício, redução drástica nos impactos ambientais, algo que os softwares de simulação podem contribuir, sobretudo na indústria metal-mecânica.
|
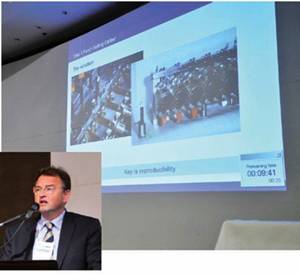
“Novas tendências de inovação em prensas para conformação a frio”, de Alexander Jansseune, Nedschroef Machinery (Bélgica), mostrou que em tempos de grande competição entre as empresas, os avanços tecnológicos são a resposta para garantir alta produtividade, versatilidade e o aumento da receita e dos resultados.
Flexibilidade sempre foi um dos maiores interesses para fabricantes de elementos de fixação e peças conformadas a frio. Troca rápida de ferramentas é a chave para este problema, viabilizando fabricação de lotes pequenos e aumentando a produtividade. O tempo de total de troca é muito maior que a chamada troca rápida de ferramentas. Trata-se de obter reprodutibilidade e vai do momento que se para de estampar o produto, até a retomada de produção com a nova peça. É uma questão de organização, ferramentas e funcionalidades para configuração dos produtos na máquina.
Um exemplo mostrado pela empresa para aprimorar a reprodutibilidade do produto foi a adoção dos seguintes recursos de ajuste rápido do ferramental: Transfer Neddrive - “troca da configuração das pinças do transfer em um toque”; Centragem rápida dos punções - “a chave é a reprodutibilidade”; Motor de avanço “é mais que apenas mover a máquina lentamente”; Cunhas especiais com controles de posição ajustáveis de regulagem rápida; Sistema de troca do bloco dos punções; Sistema de corte Nedshare, “corte de alta precisão”.
|
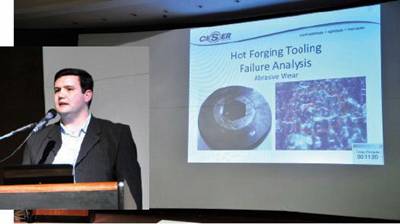
“Estudo de mecanismos de falhas no processo de forjamento a quente”, por Ricardo Blau, da Ciser Parafusos e Porcas, detalhou o forjamento a quente utilizado para a fabricação de componentes de grande complexidade e/ou de grande massa ou materiais com altos teores de carbono. Como em qualquer processo de fabricação, existem mecanismos de falha característicos atuantes nas ferramentas empregadas sendo mais comum o desgaste abrasivo, fadiga térmica e a deformação plástica. O objetivo do trabalho foi estudar alguns destes mecanismos de falha com o intuito de apresentar técnicas para minimizar ou eliminar seus respectivos efeitos.
O trabalho concluiu que: a aplicação de tecnologias de engenharia de superfícies pode aumentar drasticamente a vida útil das ferramentas; a quantidade, o tipo de fluido de refrigeração, o posicionamento e direcionamento do jato de fluido são primordiais para o bom funcionamento do processo; e a solução de problemas se inicia pelo estudo e entendimento dos mecanismos de falhas atuantes no processo.
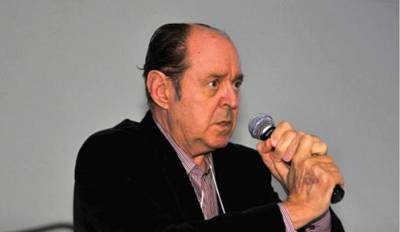
“Custo Brasil x Custo China: estudo comparativo”, por Paulo Regner, um dos idealizadores do Senafor, colocou em pauta algumas ações que podem revitalizar nossa capacidade de competição com o mercado externo, como a busca - através da inovação - pela redução de tempo em processos como o tratamento térmico, redução de set-up, implantação do terceiro turno. O objetivo é aproveitar o capital material, uma vez que uma máquina parada nada rende, concluindo com a criação de um banco de dados para compartilhamento tecnológico entre centros de desenvolvimentos de empresas.
|
|
“Simulação numérica da evolução de defeitos superficiais durante o forjamento a frio”, apresentado pelo professor Paulo Cetlin, da Universidade Federal de Minas Gerais, mostrou o estudo de fraturas superficiais no material causadas pelo seu forjamento a frio, que comumente ocorrem a partir de efeitos superficiais pré-existentes na matériaprima e que foram modificados geometricamente pela trefilação prévia ao forjamento a frio. O trabalho descreve, experimental e numericamente, a geometria inicial de defeitos após a etapa de trefilação e simula numericamente o recalque a frio de material contendo tais defeitos. Os resultados indicaram que a previsão numérica da ocorrência da abertura dos defeitos pré existentes na matéria-prima, por meio do método de elementos finitos, é uma alternativa técnica para a produção e uma melhora da qualidade dos processos produtivos, onde o recalcamento a frio é empregado.
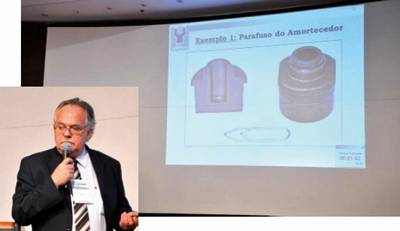
“Aspectos gerais da conformação a frio no Brasil”, por Pedro Schmitt, da Açopeças, lembrou que o Brasil tem os carros mais caros do planeta, sendo o 5º maior fabricante mundial, produzindo 50% do aço na América Latina (quase 3% do aço mundial) e 20% do minério de aço mundial. Foram apresentados cases de conformação mecânica, dentre eles um parafuso de amortecedor que teve sua produção reduzida para um único estágio, resultado obtido a partir da utilização do software eesyform. Ações como esta são exemplos da busca da otimização de processos produtivos como diferencial competitivo, reduzindo assim o número de operações set-up, entre outros.
|

“Simulação numérica para predição de evolução microestrutural em forjamento a quente”, do Dr. Shi Hong Zhang, do Institute of Metal Research, Chinese Academy of Sciences (China), apresentou um estudo onde dois tipos de titânio estão sendo usados em aplicações com elevadas temperaturas, sobretudo na indústria de motores destinados à aviação, devido ao seu excelente comportamento nessas situações.
|
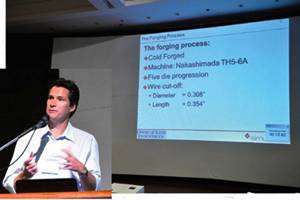
“Desenvolvimento de manufatura de rebites por simulação com Simufact.forming”, por Arjaan Buijk, da Simufact–Americas (EUA), apresentou um trabalho escrito em co-autoria com a fabricante de componentes de precisão através de forjamento a frio, a Omni-Lite (EUA). O caso representa um dos nove pedidos obtidos pela empresa no primeiro trimestre de 2011, com prazo para desenvolvimento de protótipos até o final do ano. O desafio fez com que a empresa licenciasse e empregasse o software Simufact.forming, propiciando a otimização do processo de manufatura de um dos novos componentes, com redução significativa da quantidade de try-outs.
|
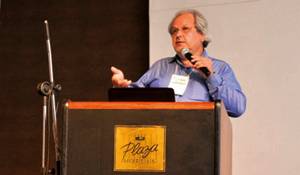
“Diferentes abordagens para determinação da microestrutura em simulação de conformação maciça de metais”, por Gerhard Arfmann, da CPM GmbH (Alemanha), tratou sobre o avanço tecnológico relativo aos softwares de simulação de processos de conformação, baseados no Método de Elementos Finitos.
Para descrever o comportamento dos materiais, esses softwares utilizam as curvas de escoamento, que são uma função da temperatura, taxas de deformação e deformação, assumindo como elemento variável a própria deformação. O procedimento não é totalmente correto porque a deformação não é independente do “caminho” para se obter um certo valor, ou seja, um mesmo valor de deformação pode corresponder a diferentes condições do material Essa deficiência pode ser superada tomando-se diretamente a microestrutura do material como base para determinar o seu comportamento, por exemplo, a densidade de deslocamento. Desta forma, ampliase os resultados clássicos mostrados pelos softwares de simulação como ‘forma final da peça conformada’, ‘deformação’, ‘cargas’ e ‘tensões’, pois conseguese também resultados precisos de ‘tamanho de grão recristalizado (dinâmica e estáticamente)’, ‘proporção de material recristalizado e não recristalizado’, ‘número e tamanho de precipitados’, ‘tamanho de grão médio’, bem como suas distribuições locais no componente forjado final.
|
“Influência do número de etapas de conformação na evolução microestrutural e nas propriedades mecânicas da liga Mg AZ61 forjada”, da professora Ana Reis, da Universidade do Porto (Portugal), relatou que uma liga Mg AZ61 foi forjada em diferentes números de etapas de conformação com temperaturas variadas. A influência do número de etapas na evolução microestrutural e nas propriedades mecânicas da liga foi estudada. Uma mesma peça de trabalho foi forjada isotermicamente em uma e três etapas, com temperatura de processo decrescendo gradativamente de 350 °C até 250°C, com redução de 50°C por etapa. Foram forjadas ainda peças em três etapas de deformação, com temperaturas constantes de 350°C e 250°C. Os resultados revelaram que os melhores valores de propriedades mecânicas finais da peça foram encontrados quando se deformou em múltiplas etapas com diminuição gradativa de temperatura. O segundo melhor desempenho foi obtido no forjamento em etapa única, com temperatura de 300°C. Os resultados obtidos com a deformação dividida em três etapas, mantendo-se a temperatura constante em 350°C ficaram abaixo dos dois primeiros. Por fim, a deformação em três etapas, com temperaturas de 250°C, não foi bem-sucedida, apresentando trincas logo na segunda etapa de conformação. As rotas processadas em etapa única em 350°C e três etapas com temperatura constantes também de 350°C apresentaram grãos parcialmente recristalizados, fenômeno que não se verificou nos forjamentos em temperaturas mais baixas.
|
“Produtos de revestimento avançado para conformação a frio com aplicação em linha contínua, curta e simplificada”, por Peter Zwez, da Zwez-Chemie GmbH (Alemanha), demonstrou que a aplicação de um revestimento de fosfato de zinco, combinado com um lubrificante adequado, ainda é o tratamento de superfície mais utilizado antes de processos de conformação a frio. O processo exige um grande número de tanques, incluindo os de lavagem, que gasta muito tempo e elevado consumo de água. A redução de etapas desses processos indica vantagens comerciais e ambientais. A empresa dispõe de produtos desenvolvidos para esta aplicação, onde a vida útil é quase ilimitada, sendo possível obter economia de energia e tempo de 75% a 90%.
|
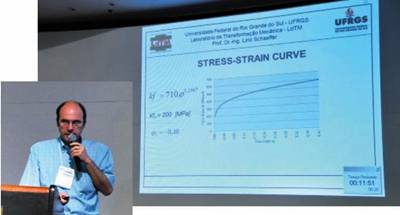
“Simulação numérica do processo de extrusão através do software I-Form”, por Luiz Cavaler, da Faculdade SATC, analisou as forças de compressão obtidas por métodos empíricos de cálculos e pela Teoria Elementar da Plasticidade, e confrontou os valores com simulações numéricas realizadas pelo método de elementos finitos (FEM) empregando o software I-Form 2D. Os valores de força de compressão medidos experimentalmente foram utilizados na comparação com valores obtidos por meio da simulação computacional para validação dos valores calculados pelo software. As simulações basearam-se no processo de compressão uniaxial e empregou-se o aço DIN Ck15 nos ensaios. Foram realizados três ensaios com coeficientes de atrito diferentes. Os resultados foram semelhantes aos cálculos apresentados na literatura dentro de uma faixa de erro máximo de 15%. Nas simulações realizadas, observou-se que na medida em que o coeficiente de atrito é aumentado, o valor da diferença entre a força de compressão pelos três métodos também é maior.
|
|
|
|